Galvanised Sheeting
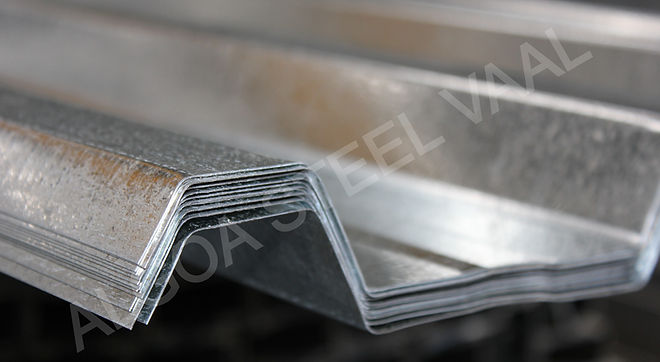
Available in IBR, Widespan & Corrugated profile cut to any length as per customers' requirements
Gauges available (thickness of steel)
0.30 mm
0.35mm
0.40 mm
0.47 mm
0.50 mm
0.58mm
0.80 mm
IBR Coverage
686mm
686mm
686mm
686mm
686mm
686mm
686mm
Widespan Coverage
752mm
752mm
752mm
752mm
752mm
752mm
752mm
Corrugated Coverage
762mm
762mm
762mm
762mm
762mm
762mm
762mm
Metallic coated sheet, specifically continuously hot-dip zinc-coated (galvanised) sheet, is a well-known product with a versatile range of applications in general industry, buildings, construction and appliances.
As the name implies, continuous hot-dip coating involves the application of a molten coating onto the surface of steel sheet (cold- or hot rolled) in a non-stop process.
In this process a material is produced with strength/formability properties provided by the steel substrate and the corrosion protection by the zinc coating.
The zinc coating (layer) protects the steel by providing a barrier to elements in an exposed environment through the sacrificial nature of zinc (cathodic protection).
Expected service life depends on coating thickness and the aggressiveness of the exposed environment.
The zinc coating protects the steel substrate in two ways:
​
1. by providing a barrier between the steel and the environment and
2. through galvanic protection.
When zinc is exposed to the environment in a wet/dry cycle a relatively stable (insoluble in water) zinc oxide/carbonate protective layer is formed through the reaction of zinc with oxygen, water and carbon dioxide.
This is the primary reason for the low corrosion rate of zinc in most environments.
Zinc is more electro-negative than steel in the galvanic series and will sacrificially corrode when the base steel is exposed, at a cut edge or scratch.
Material with a total coated thickness of less than 2.50 mm is adequately protected along cut edges by a Z275 coating.
However, the zinc oxide/carbonate layer tends to dissolve when the surface moisture film is sufficiently acidic or alkaline (oxide relatively stable in pH range 6-12.5).
The specific environment i.e. agricultural, industrial, and coastal and others could influence actual performance.
In general, with thicker the zinc coatings, greater protection will be provided in specific environments.
It is recommended that galvanised sheeting be over-painted before the formation and first appearance of red corrosion products.
Handling & Protection
Zinc reacts with the environment to form a continuous passive layer of a protective oxide/carbonate in a wet/dry cycle.
It is important that a zinc coated surface when wet is exposed to adequate ventilation and dries in free flowing air to develop this layer.
Wet storage staining (also known as white rust) is formed when the reactive zinc, on two surfaces in close proximity, in contact with moisture and without exposure to CO2 (drying cycle), form the chemical compound- zinc hydroxide (ZnOH).
​
The extent of the formation of wet storage stain is dependent on:
1. Exposure time to moisture,
2. Temperature experienced during exposure and
3. Contaminants (i.e. Chlorine salts) that could accelerate the reaction.
​
The key is that galvanised surfaces, in close proximity, must be kept dry at all times during transport and storage, all necessary precautions must be taken to prevent the formation of condensation or ingress of moisture between surfaces.
Packs of galvanised material must not be stacked directly on floors.
Rainwater or water vapour can easily be drawn in between tightly stacked profiled or flat sheets, or between laps of coils by capillary action.
Due to the absence of freely circulating air, this moisture cannot evaporate, causing unfavourable conditions that may result in wet storage staining of the galvanised material.
Welding
Zinc coated steels may be welded satisfactorily by the most commonly practised welding techniques. Weld spatter should be avoided, to ensure no damage to the zinc coated surface.
Spatter will act as preferential sites for corrosion.
Closer control of welding parameters and welding in adequately ventilated areas is necessary to reduce the effect of toxic fumes when welding galvanised steel.
Painting
Chemical conversion coatings and primers have been developed to provide good adhesion of subsequent paint films applied to zinc-coated surfaces.
To obtain optimum results it is essential to adhere to the instructions of the paint manufacturers.
Galvanised Sheeting Life Expectancy
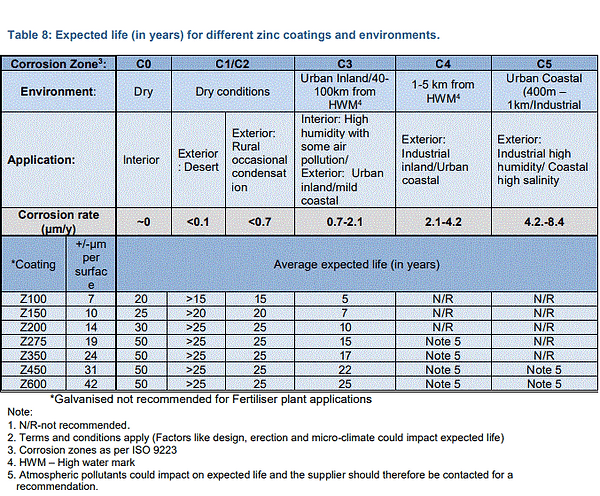